Mill liners and grinding balls are essential components in the operation of ball mills. With the development of modern production technologies, the diameters of ball mills have increased, with mills around 5 meters in diameter now commonly used. This growth has led to higher demands for the quality of liners and grinding balls. Due to the harsh operating conditions that liners and grinding balls are exposed to, maintenance and replacement costs are high, which not only wastes labor and resources but also directly impacts production efficiency. Therefore, researching new wear-resistant materials for liners and grinding balls is key to improving productivity, reducing consumption, and fostering a more efficient and environmentally-friendly production process.
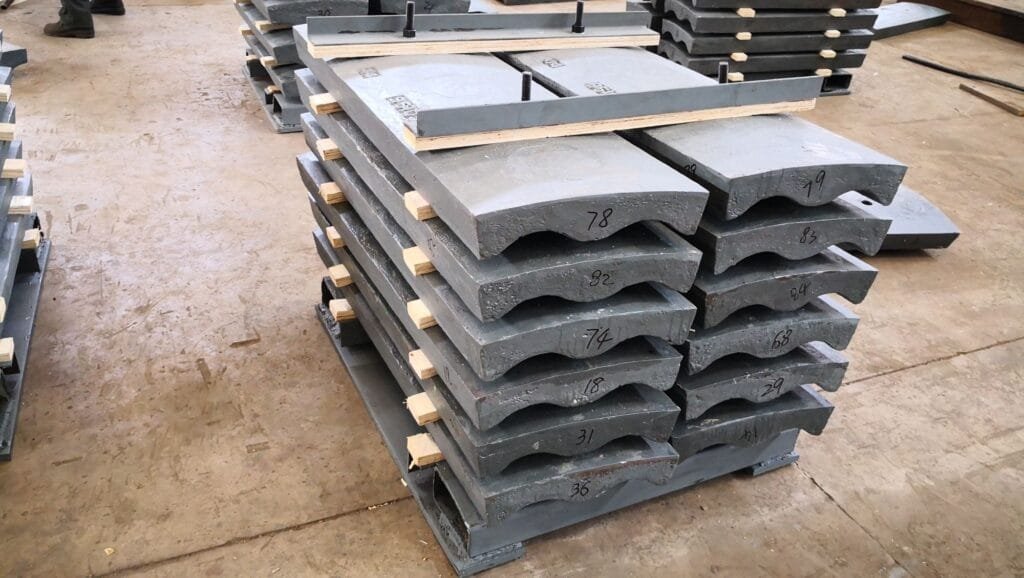
1. Understanding Ball Mill Liners
Traditional high-manganese steel is no longer suitable for ball mill liners. This is widely recognized in the industry. The disadvantages of high-manganese steel liners include susceptibility to creep and extension, as well as surface phase transformations that cause bowing deformation. These issues make it impossible to achieve the ideal work-hardening effect in the harsh conditions of a ball mill. The former leads to powder leakage and broken bolts, while the latter prevents the expected wear resistance.
In the 1970s and 1980s, various high-hardness liner and grinding ball materials were introduced, such as high-chromium cast iron, nickel-hard cast iron, high-carbon alloy steel, martensitic ball iron, and some medium-carbon alloy steels. However, these materials had low toughness values—some as low as 5J. Due to the limitations imposed by traditional liner designs, these materials were not widely adopted. Liner breakage has become the biggest obstacle to the application of high-hardness, wear-resistant materials.
The traditional liner designs are fundamentally flawed and cannot accommodate the development of wear-resistant materials. The two main types of liner installation structures are: one used in thermal power plants with dovetail grooves and wedge screws, and the other widely used in mining, cement, chemical industries, and large power plants, where each liner is bolted to the drum. The former design, while potentially effective in some cases, leads to the rapid wear of wedge screws, which are the most unstable fastening method. The latter design, involving numerous drilled holes and bolts, creates potential leak points and increases labor intensity. These designs are clearly flawed, especially considering that fastening the liners with holes creates numerous crack sources during the casting and heat treatment process.
The “Self-Fixing, Bolt-Free” Composite Ball Mill Liner
In response to the shortcomings of traditional designs, we have developed the “Composite Self-Fixing, Bolt-Free Ball Mill Liner,” a revolutionary product that marks a major breakthrough in ball mill liner design. This composite liner is made up of two or three independent parts: a high-hardness alloy body for wear resistance and a tough alloy backplate that stabilizes the liner and applies pre-stress to the body.
By utilizing the geometry of the mill itself and employing a dual-metal combination, the composite liner uses the grinding balls’ action during operation to apply pre-stress, achieving self-fixing and enhancing the overall structural integrity of the liner. This design significantly improves the stability and reliability of high-hardness, low-toughness material liners.
The manufacturing and installation processes for composite liners are simpler than traditional liners, requiring no modifications to existing mills. Over the past 20 years, this innovative liner design has been successfully applied in thermal power plants, cement plants, mining, and phosphate industries, proving its superior stability, reliability, and long-term performance. The maintenance requirements are minimal, and the liner can last much longer than traditional designs, contributing to reduced noise levels and a safer working environment.

2. The Importance of Grinding Balls
Grinding balls used in ball mills are typically made from high-carbon high-alloy cast iron or high-carbon low-alloy forged or cast balls. In dry processes, such as those used in thermal power plants and cement industries, high-chromium cast iron balls are commonly used, while mining operations, which typically use wet processes, often use high-carbon low-alloy balls.
The variety of grinding balls on the market is vast, and in some cases, the choice of balls is not made based on process efficiency but rather based on availability and cost. The main types of grinding balls include high-chromium cast iron balls (e.g., Cr8, Cr12, Cr15, Cr18, Cr24) and low-chromium cast iron balls. Martensitic ball iron and low-chromium cast iron balls provide similar wear resistance, but the main difference lies in the production process.
High-chromium cast iron grinding balls offer excellent wear resistance, with the wear rate in power plants and cement plants typically ranging from 15 to 50 grams per ton. The use of high-chromium balls not only reduces costs but also minimizes labor and electricity consumption, making them an environmentally friendly choice. We can confidently call them “green grinding balls.”
For mining applications, especially for wet processes, low-chromium alloy balls are commonly used. These balls are typically in the range of 500-700 grams per ton in copper, iron, and molybdenum mining operations. By improving the hardness of low-chromium balls (e.g., achieving HRC55), wear resistance can be significantly improved.
3. The Relationship Between Mill Liners and Grinding Balls
A commonly held misconception is that grinding balls should have a hardness that is 3-5 HRc higher than that of the liners. However, in reality, the liner plays a much more significant role in the operation of the ball mill. The primary focus should be on ensuring that the liner has a long service life, ideally two overhaul cycles, with minimal maintenance.
Choosing the right material for both the liners and grinding balls is essential. For liners, materials such as composite self-fixing high-chromium cast iron liners should be prioritized for their long service life and reliability. For grinding balls, the best wear-resistant balls should be selected to match the liner material.
It is critical to choose liners with a hardness greater than HRc50, as this ensures optimal wear resistance. High-chromium cast iron or forged alloy steel grinding balls with a hardness greater than HRc52 (cast) or HRc55 (forged) are the ideal choice for ensuring the longevity of the entire grinding system.

4. Conclusion
High-Manganese Steel and Traditional Liner Designs: These are not suitable for modern ball mills. The revolutionary design of the composite self-fixing liner effectively solves issues such as bolt breakage and powder leakage, reducing maintenance by over 98%. It maximizes the hardness and wear resistance of materials, achieving optimal grinding performance.
Liner and Grinding Ball Material Selection: In dry processes, power plants and cement plants should prioritize medium- and low-chromium alloy steel or high-chromium cast iron liners, paired with high-hardness high-chromium cast iron grinding balls. In mining applications, low-carbon alloy steel liners or low-chromium cast iron liners should be chosen, with high-hardness low-chromium alloy grinding balls.
Matching Liners and Grinding Balls: The liner is the primary factor in determining the grinding efficiency of the mill. Choosing the right liners with a service life of at least two overhaul cycles allows for better selection of grinding balls. Ideally, liners and grinding balls should be chosen to maintain optimal performance for the longest possible period.