Pelapis pabrik dan bola gerinda adalah komponen penting dalam pengoperasian ball mill. Dengan perkembangan teknologi produksi modern, diameter ball mill telah meningkat, dengan diameter ball mill sekitar 5 meter yang sekarang umum digunakan. Pertumbuhan ini telah menyebabkan tuntutan yang lebih tinggi untuk kualitas liner dan bola gerinda. Karena kondisi operasi yang keras yang dihadapi oleh liner dan grinding ball, biaya perawatan dan penggantian menjadi tinggi, yang tidak hanya membuang tenaga kerja dan sumber daya, tetapi juga secara langsung berdampak pada efisiensi produksi. Oleh karena itu, meneliti material baru yang tahan aus untuk liner dan grinding ball merupakan kunci untuk meningkatkan produktivitas, mengurangi konsumsi, dan mendorong proses produksi yang lebih efisien dan ramah lingkungan.
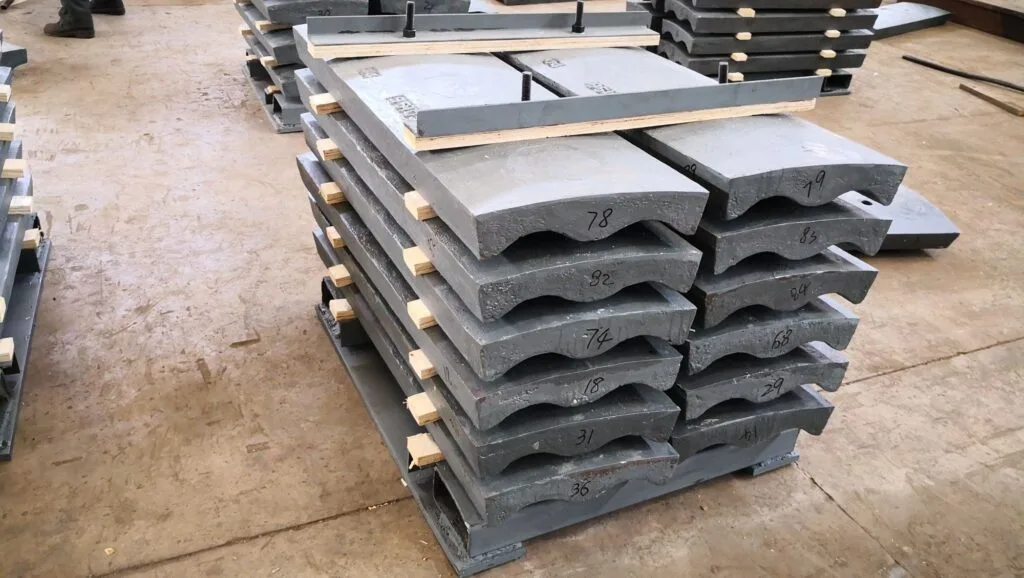
1. Memahami Ball Mill Liners
Baja mangan tinggi tradisional tidak lagi cocok untuk pelapis ball mill. Hal ini diakui secara luas di industri. Kerugian dari lapisan baja mangan tinggi termasuk kerentanan terhadap creep dan ekstensi, serta transformasi fase permukaan yang menyebabkan deformasi busur. Masalah-masalah ini membuat tidak mungkin untuk mencapai efek pengerasan kerja yang ideal dalam kondisi ball mill yang keras. Yang pertama menyebabkan kebocoran bubuk dan baut yang patah, sedangkan yang kedua mencegah ketahanan aus yang diharapkan.
Pada tahun 1970-an dan 1980-an, berbagai material liner dan bola gerinda dengan kekerasan tinggi diperkenalkan, seperti besi cor kromium tinggi, besi cor nikel-keras, baja paduan karbon tinggi, besi bola martensit, dan beberapa baja paduan karbon sedang. Namun, material-material ini memiliki nilai ketangguhan yang rendah-beberapa di antaranya serendah 5J. Karena keterbatasan yang diberlakukan oleh desain kapal tradisional, material ini tidak diadopsi secara luas. Kerusakan liner telah menjadi hambatan terbesar dalam penerapan material dengan kekerasan tinggi dan tahan aus.
Desain liner tradisional pada dasarnya memiliki kelemahan dan tidak dapat mengakomodasi pengembangan material tahan aus. Dua jenis utama struktur pemasangan liner adalah: satu digunakan di pembangkit listrik tenaga panas dengan alur pas dan sekrup baji, dan yang lainnya banyak digunakan di pertambangan, semen, industri kimia, dan pembangkit listrik besar, di mana setiap liner dibaut ke drum. Desain yang pertama, meskipun berpotensi efektif dalam beberapa kasus, menyebabkan keausan yang cepat pada sekrup baji, yang merupakan metode pengencangan yang paling tidak stabil. Desain yang terakhir, yang melibatkan banyak lubang dan baut yang dibor, menciptakan titik kebocoran potensial dan meningkatkan intensitas tenaga kerja. Desain ini jelas memiliki kekurangan, terutama mengingat bahwa mengencangkan liner dengan lubang menciptakan banyak sumber retakan selama proses pengecoran dan perlakuan panas.
Liner Ball Mill Komposit "Memperbaiki Sendiri, Bebas Baut"
Menanggapi kekurangan desain tradisional, kami telah mengembangkan "Ball Mill Liner Komposit yang Dapat Mengunci Sendiri dan Bebas Baut," sebuah produk revolusioner yang menandai terobosan besar dalam desain ball mill liner. Liner komposit ini terdiri dari dua atau tiga bagian independen: bodi paduan dengan kekerasan tinggi untuk ketahanan aus dan pelat belakang paduan tangguh yang menstabilkan liner dan memberikan tekanan awal pada bodi.
Dengan memanfaatkan geometri dari pabrik itu sendiri dan menggunakan kombinasi logam ganda, liner komposit menggunakan aksi bola gerinda selama operasi untuk menerapkan pra-stres, mencapai pengencangan sendiri dan meningkatkan integritas struktural liner secara keseluruhan. Desain ini secara signifikan meningkatkan stabilitas dan keandalan liner material dengan kekerasan tinggi dan ketangguhan rendah.
Proses pembuatan dan pemasangan liner komposit lebih sederhana daripada liner tradisional, sehingga tidak memerlukan modifikasi pada pabrik yang sudah ada. Selama 20 tahun terakhir, desain liner yang inovatif ini telah berhasil diterapkan di pembangkit listrik tenaga panas, pabrik semen, pertambangan, dan industri fosfat, yang membuktikan stabilitas, keandalan, dan kinerja jangka panjangnya yang unggul. Persyaratan perawatannya minimal, dan liner ini dapat bertahan lebih lama daripada desain tradisional, sehingga mengurangi tingkat kebisingan dan lingkungan kerja yang lebih aman.

2. Pentingnya Bola Gerinda
Bola gerinda yang digunakan dalam ball mill biasanya terbuat dari besi tuang paduan tinggi karbon tinggi atau bola tempa atau bola tuang paduan rendah karbon tinggi. Dalam proses kering, seperti yang digunakan di pembangkit listrik tenaga panas dan industri semen, bola besi tuang berkromium tinggi biasanya digunakan, sementara operasi penambangan, yang biasanya menggunakan proses basah, sering menggunakan bola paduan rendah karbon tinggi.
Variasi bola gerinda yang ada di pasaran sangat banyak, dan dalam beberapa kasus, pilihan bola tidak dibuat berdasarkan efisiensi proses, melainkan berdasarkan ketersediaan dan biaya. Jenis utama bola gerinda meliputi bola besi tuang berkromium tinggi (misalnya, Cr8, Cr12, Cr15, Cr18, Cr24) dan bola besi tuang berkromium rendah. Bola besi martensit dan bola besi tuang kromium rendah memberikan ketahanan aus yang serupa, tetapi perbedaan utamanya terletak pada proses produksi.
Bola gerinda besi tuang kromium tinggi menawarkan ketahanan aus yang sangat baik, dengan tingkat keausan di pembangkit listrik dan pabrik semen biasanya berkisar antara 15 hingga 50 gram per ton. Penggunaan bola berkromium tinggi tidak hanya mengurangi biaya, tetapi juga meminimalkan konsumsi tenaga kerja dan listrik, sehingga menjadi pilihan yang ramah lingkungan. Kami dengan yakin dapat menyebutnya sebagai "bola gerinda hijau".
Untuk aplikasi pertambangan, terutama untuk proses basah, bola paduan kromium rendah biasanya digunakan. Bola-bola ini biasanya berkisar antara 500-700 gram per ton dalam operasi penambangan tembaga, besi, dan molibdenum. Dengan meningkatkan kekerasan bola kromium rendah (misalnya, mencapai HRC55), ketahanan aus dapat ditingkatkan secara signifikan.
3. Hubungan Antara Mill Liners dan Grinding Balls
Kesalahpahaman yang umum dipegang adalah bahwa bola gerinda harus memiliki kekerasan 3-5 HRc lebih tinggi daripada liner. Namun, pada kenyataannya, liner memainkan peran yang jauh lebih signifikan dalam pengoperasian ball mill. Fokus utama harus memastikan bahwa liner memiliki masa pakai yang lama, idealnya dua siklus perombakan, dengan perawatan minimal.
Memilih material yang tepat untuk liner dan bola gerinda sangatlah penting. Untuk liner, material seperti liner besi cor kromium tinggi yang dapat dipasang sendiri oleh komposit harus diprioritaskan karena masa pakai dan keandalannya yang lama. Untuk bola gerinda, bola tahan aus yang terbaik harus dipilih agar sesuai dengan bahan pelapis.
Sangat penting untuk memilih liner dengan kekerasan yang lebih besar dari HRc50, karena hal ini memastikan ketahanan aus yang optimal. Bola gerinda besi tuang kromium tinggi atau bola gerinda baja paduan yang ditempa dengan kekerasan yang lebih besar dari HRc52 (tuang) atau HRc55 (tempa) adalah pilihan yang ideal untuk memastikan masa pakai yang lama pada seluruh sistem gerinda.

4. Kesimpulan
Baja Mangan Tinggi dan Desain Kapal Tradisional: Ini tidak cocok untuk pabrik bola modern. Desain revolusioner dari komposit self-fixing liner secara efektif memecahkan masalah seperti kerusakan baut dan kebocoran bubuk, mengurangi perawatan lebih dari 98%. Ini memaksimalkan kekerasan dan ketahanan aus material, mencapai kinerja penggilingan yang optimal.
Pemilihan Bahan Liner dan Bola Gerinda: Pada proses kering, pembangkit listrik dan pabrik semen harus memprioritaskan baja paduan kromium sedang dan rendah atau pelapis besi tuang kromium tinggi, yang dipasangkan dengan bola gerinda besi tuang kromium tinggi dengan kekerasan tinggi. Dalam aplikasi pertambangan, pelapis baja paduan rendah karbon atau pelapis besi tuang rendah kromium harus dipilih, dengan bola gerinda paduan kromium rendah kekerasan tinggi.
Mencocokkan Liner dan Bola Gerinda: Liner adalah faktor utama dalam menentukan efisiensi penggilingan pabrik. Memilih liner yang tepat dengan masa pakai minimal dua siklus overhaul memungkinkan pemilihan bola gerinda yang lebih baik. Idealnya, liner dan bola gerinda harus dipilih untuk mempertahankan kinerja yang optimal untuk jangka waktu yang paling lama.