Ball mill liners are vital components in cement plant operations, as they protect the mill shell from wear and contribute to efficient grinding. Replacing these liners at the right time and with the right materials can significantly enhance the performance and longevity of the mill. In this article, we’ll discuss the key considerations for ball mill liner replacement in cement plants to help you make informed decisions and ensure smooth operations.
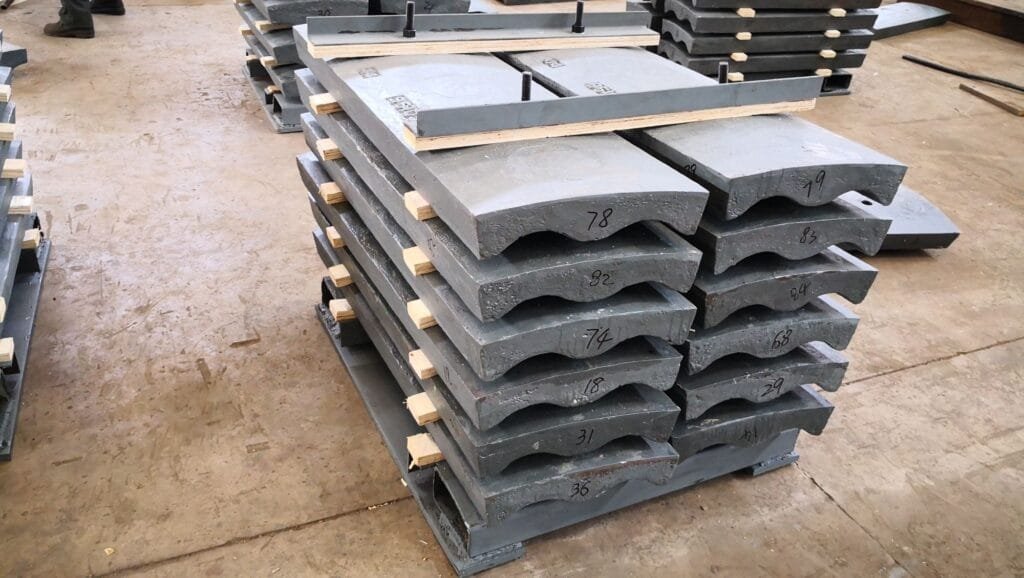
1. Liner Material Selection
Choosing the correct material for ball mill liners is crucial for optimizing the mill’s performance and minimizing wear. The right material should be compatible with the specific conditions of your cement plant, including the type of material being ground and the operating environment.
- High-Manganese Steel: Best for mills that handle abrasive materials, offering high impact and wear resistance.
- Chrome Alloy Steel: Suitable for mills where corrosive materials are processed, as it provides better resistance to chemical wear.
- Rubber Liners: Often used in lower-speed mills for better shock absorption and quieter operation.
2. Mill Liner Design
The design of the ball mill liner affects the grinding efficiency, energy consumption, and overall performance. Custom-designed liners can optimize mill operations, improving the grinding media motion and reducing power consumption.
- Wave Liners: Designed to promote cascading grinding media motion, enhancing grinding efficiency.
- Step Liners: Offer a smooth trajectory for grinding media, improving output and reducing wear.
- Segmented Liners: Provide ease of replacement and can be customized based on specific grinding conditions.
3. Timing of Ball Mill Liner Replacement
Replacing ball mill liners at the right time is essential to avoid downtime and prevent damage to other mill components. Regular inspections and monitoring of wear patterns will help determine the best time for replacement.
- Signs for Replacement: Excessive wear, visible cracks, uneven wear patterns, and reduced grinding efficiency are indicators that the liners need replacement.
- Preventive Maintenance: Regularly inspect and monitor liner wear through visual inspections and use of ultrasonic testing or wear analysis to avoid unexpected breakdowns.
4. Mill Speed and Load Impact
Mill speed and the load of grinding media significantly impact the wear rate of liners. If the mill operates at a higher speed or load than recommended, it can accelerate liner wear and reduce the lifespan.
- Optimized Mill Speed: Maintain the recommended speed to avoid unnecessary stress on the liners.
- Proper Load Balance: Ensure the correct distribution of grinding media to prevent uneven wear and excessive liner stress.
5. Cost vs. Performance
While liner replacement can be a significant expense, choosing liners that provide better performance and longer service life can lead to long-term savings. It’s essential to balance the upfront costs of high-quality liners with their potential to improve grinding efficiency and reduce maintenance costs.
- Higher Initial Costs for Long-Term Gains: Investing in high-quality liners with longer lifespans can reduce downtime and maintenance costs over time.
- Energy Efficiency: Well-designed liners reduce energy consumption, offering significant cost savings over time.
6. Supplier Selection and Support
Choosing a reliable supplier is key to ensuring that you get the best liners for your ball mill. A reputable supplier will not only provide high-quality products but also offer technical support, liner customization, and after-sales services.
- Reputation and Experience: Select a supplier with a proven track record and experience in the cement industry.
- Technical Support: Ensure the supplier provides guidance on liner selection, installation, and maintenance.
Conclusion
Replacing ball mill liners in cement plants is a critical task that requires careful consideration of factors such as material selection, liner design, timing, mill speed, and cost-effectiveness. By focusing on these key factors, you can optimize your mill’s performance, extend the lifespan of your equipment, and reduce operational costs. Regular inspections and working with trusted suppliers will ensure that your ball mill continues to operate at peak efficiency.
Looking for expert advice on ball mill liner replacement? Contact us today to explore our high-quality liner solutions tailored to your cement plant’s needs!