The Importance of High-Quality Crusher Hammers
The crusher hammer is one of the most crucial working components in a crusher. A high-quality, wear-resistant hammer is essential for ensuring the crusher’s normal operation. The lifespan of the crusher hammer depends on its material quality and the characteristics of the materials being crushed. These factors directly impact the efficiency of the crusher.
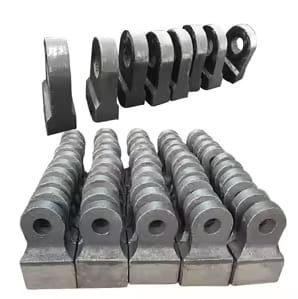
Common Materials for Crusher Hammers
In the mining machinery industry, crusher hammers are typically made from several materials, each with its own advantages and drawbacks. The most commonly used hammer materials include:
1. High Manganese Steel
High manganese steel is a traditional material for manufacturing crusher hammers. It is known for its impact wear resistance and high toughness. One of its key features is its work hardening capability—under impact or contact stress, the surface rapidly hardens, improving wear resistance significantly.
However, high manganese steel only exhibits superior wear resistance under sufficient impact force. If the physical impact is not strong enough, the surface does not undergo the necessary hardening process, resulting in poor wear resistance.
2. Medium Manganese Steel
Medium manganese steel provides a cost-effective alternative to high manganese steel while achieving similar performance. Its advantages include:
Longer service life—50% more than traditional high manganese steel hammers.
Magnetic properties—allowing easy removal of iron debris from ores, which high manganese steel lacks.
3. High Chromium Cast Iron
High chromium cast iron is well-known for its excellent wear resistance. However, it has low toughness, making it prone to brittle fractures. To enhance its durability, composite hammers have been developed. These combine high chromium cast iron in the hammer’s working area with high manganese steel or low alloy steel in the hammer body, providing both hardness and toughness.
4. Low Carbon Alloy Steel
Low carbon alloy steel contains elements such as chromium and molybdenum, offering:
High hardness and excellent toughness
Extended service life—at least twice that of high manganese steel hammers
However, its manufacturing process is complex, requiring precise heat treatment. The hammer must achieve a tensile strength of over 850 MPa while maintaining plasticity and toughness. Additionally, to prevent iron block damage, secondary magnetic separation devices are recommended before feeding the crusher.
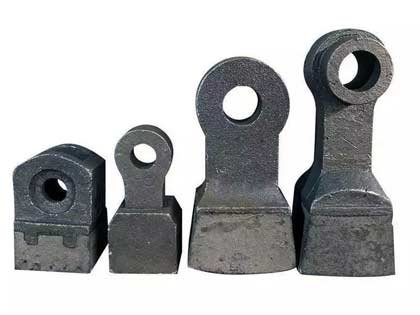
How to Select the Right Crusher Hammer
Choosing the correct crusher hammer material is crucial for maximizing performance and durability. Several factors should be considered:
1. Material Hardness vs. Hammer Hardness
The harder the material to be crushed, the higher the required hammer hardness.
Larger material chunks require hammers with greater toughness.
The balance between hardness and toughness is essential for optimal performance.
2. Crusher Specifications and Impact Load
Larger crushers require heavier hammers to handle bigger material chunks.
Higher impact loads demand hammers with superior toughness to prevent fractures.
After ensuring adequate toughness, hardness should be optimized for wear resistance.
3. Cost-Effectiveness and Market Acceptance
A hammer’s material should align with budget constraints and cost-effectiveness.
Market acceptance and application results should be evaluated before finalizing a material choice.
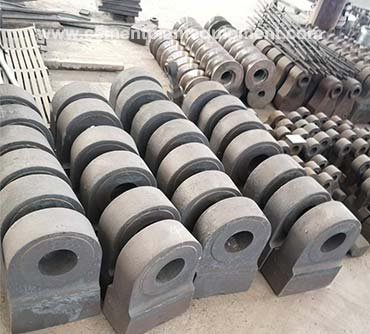
Best Practices for Hammer Maintenance
Selecting the right crusher hammer is only part of the equation. Proper usage and scientific maintenance are equally crucial in extending hammer life. Some key maintenance strategies include:
Regular inspections to identify and replace worn-out hammers promptly.
Ensuring proper feeding practices to avoid excessive impact forces.
Implementing secondary iron removal systems to prevent metal contamination.
By selecting the right crusher hammer material and following best maintenance practices, you can significantly enhance your crusher’s performance, reduce downtime, and extend equipment lifespan. Investing in high-quality hammers tailored to your operational needs is a cost-effective strategy for improving overall efficiency.