When it comes to stone production and sand pits, large hammer crushers are indispensable. The crusher hammers used in these crushers come in a variety of materials, and it’s often unclear which ones are the most durable. What are the commonly used hammer head materials, and which ones have the best wear resistance? In this article, ECONE Industrial Co., Ltd. will introduce several types of hammer crusher hammers and explain which materials are the most durable and commonly used.
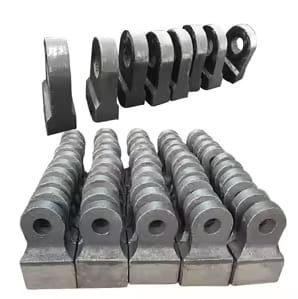
What Are Hammer Crusher Hammers?
In stone production, hammers are the most easily worn components of hammer crushers. The quality of the hammer directly impacts the crusher’s wear resistance and, subsequently, the production efficiency of the stones. Experienced plant managers often want to know: What materials are used for hammer crusher hammers?
The commonly used materials for hammer crusher hammers in the mining machinery industry include high manganese steel, medium manganese steel, high chromium cast iron, double-liquid composite hammers, low carbon alloy steel, forged hammers, and composite alloy hammers. Each of these materials has its unique characteristics and advantages, but they also come with specific limitations.
ECONE's Expertise in Hammer Crusher Parts
ECONE Industrial Co., Ltd. has been manufacturing crusher parts for over 30 years. Our team has extensive experience in casting hammerheads, using advanced techniques like vacuum casting for high chromium alloy hammers. Our high chromium alloy hammer technology is patented, ensuring the hammer’s internal structure is dense, the alloy composition is precise, and the heat treatment process is flawless. This results in a lifespan that is 3-5 times longer than traditional manganese steel hammers. We offer high chromium hammers in stock and can customize them according to your drawings or samples. We deliver fast directly from the manufacturer.
Wear-Resistant Hammer Crusher Hammers
Hammer crusher hammers are essential for efficient operation. A high-quality, wear-resistant hammer ensures smooth and continuous operation, significantly enhancing the crusher’s efficiency. The hammer’s lifespan depends not only on its material but also on the hardness of the materials being crushed. When selecting a hammer for your crusher, it’s crucial to consider both the hammer’s wear resistance and the properties of the material to be crushed.
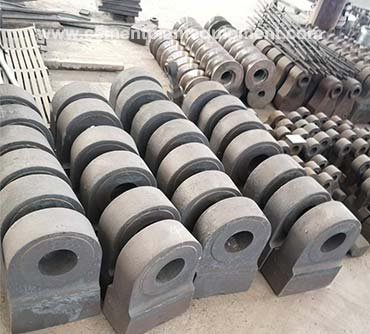
Types of Hammer Crusher Hammer Materials
High Manganese Steel Hammers
High manganese steel is the traditional material for hammer crusher hammers. It’s known for its excellent impact resistance and wear resistance. It exhibits a strong tendency for work hardening under impact conditions, significantly improving wear resistance in high-stress environments. However, its wear resistance is only optimal when the impact force is strong enough to trigger work hardening. In cases of lower impact forces or minimal contact stress, its performance may be suboptimal.
Bimetallic Composite Hammers
Bimetallic composite hammers use a special casting process to combine various alloys, such as molybdenum, vanadium, nickel, niobium, tungsten, titanium, and rare earth metals. After water quenching, the hardness reaches 62-65 HRC. These hammers offer a lifespan 3-5 times that of high manganese or forged hammers. The hammer’s head is made of high-chromium cast iron for wear resistance, while the handle uses tough manganese alloy steel, combining the advantages of both materials for exceptional durability and impact resistance. ECONE’s high-chromium composite hammers are ideal for crushing tough materials like granite, basalt, limestone, and cement clinker.
Medium Manganese Steel Hammers
Medium manganese steel hammers are gaining popularity in many mining machinery factories. They offer similar performance to ZGMn13 high manganese steel hammers but at a lower cost. These hammers improve the service life by more than 50% compared to ZGMn13, and they perform particularly well in crushing materials like sodium feldspar, where the lifespan is over 60% longer. Additionally, medium manganese steel hammers have magnetic properties, allowing iron particles to be removed via magnetic separation, which improves the quality of ceramics—a benefit that high manganese steel lacks.
High Chromium Cast Iron Hammers
High chromium cast iron is known for its excellent wear resistance, but it tends to be brittle and prone to breakage. To address this, ECONE has developed composite hammers with high chromium cast iron on the head and low-alloy steel or manganese steel for the handle. This combination enhances the hammer’s hardness and wear resistance while maintaining high toughness and impact resistance. These hammers are ideal for crushing materials like cement clinker, offering a lifespan twice as long as high manganese steel hammers.
Hard Alloy Hammers
Hard alloys are composed of metal carbides (such as WC and TiC) in powdered form, bonded together with materials like cobalt or nickel. These materials are known for their extremely high hardness, melting points, and strength. Hard alloy hammers offer superior wear resistance, impact strength, and heat resistance compared to other materials. These hammers solve common problems with high manganese steel, such as cracking, spalling, and chunking.
Forged Hammers
Forged hammers are made from manganese steel and undergo a process of repeated hammering to improve their mechanical properties. The forging process eliminates defects like porosity and optimizes the microstructure. After heat treatment, these hammers exhibit excellent wear resistance. While they are cost-effective and durable, forged hammers are being gradually replaced by other materials due to their limited performance in certain applications.
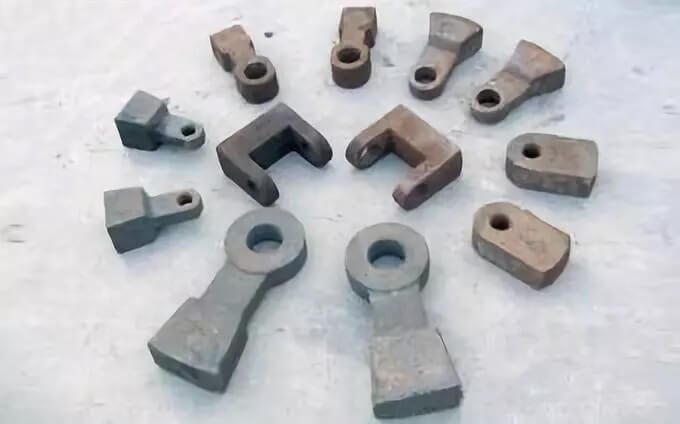
Why Material Selection Matters
Some users mistakenly assume that forged hammers are the best option because of their lower price. However, forged hammers are becoming obsolete, and many suppliers are now offering high-chromium composite hammers that outperform them in terms of durability and wear resistance. For example, some suppliers may market their products as high chromium hammers but use an inadequate chromium content, resulting in premature wear. It’s crucial to ensure that the hammer material meets the required standards to avoid premature failures and inefficiencies.
Conclusion
Understanding the materials used in hammer crusher hammers is crucial for maximizing productivity, reducing labor costs, and ensuring consistent crusher performance. By selecting the right hammer material based on the crushing application, you can improve production efficiency and extend the lifespan of your equipment. ECONE’s bimetallic composite hammers offer excellent wear resistance, impact strength, and reliability, making them ideal for tough crushing tasks. For high-quality, durable, and affordable hammers, choose ECONE INDUSTRIAL—your trusted hammer expert!