With the increasing demand for hammer heads of crushers, various large and small crusher hammer head manufacturers have emerged. For users struggling with selection, the process can be confusing. The wear and tear of the hammer head is a major problem faced by many companies. The mainstream material for hammer heads in the market is high chromium alloy. However, different crushers require different materials based on the type of material being crushed. Each type of hammer head has its own advantages. So how do you choose the right hammer head? Users need to decide based on their specific needs and budget.
Types of Crusher Hammer Heads
There are several types of hammer heads available, each made from different raw materials. The material composition greatly affects the hammer head’s performance and durability. When selecting a hammer head for a crusher, it is crucial to consider factors such as hardness, impact resistance, and longevity.
Key Factors in Choosing a Hammer Head
When selecting a crusher hammer head, the following factors should be taken into account:
Material Hardness – Harder materials require hammer heads with higher hardness.
Working Conditions – Consider whether the crusher operates under high impact or abrasive conditions.
Wear Mechanism – Some materials wear out faster than others, affecting replacement frequency.
Operating Time – The expected service life of the hammer head should align with production needs.

The Crushing Process and Wear Mechanism
Crusher hammer heads undergo a complex wear process influenced by several factors, including:
The strength, hardness, and toughness of the material being crushed.
The size, humidity, and density of the material.
External conditions such as impact forces and material distribution at the moment of crushing.
The crushing process is an irreversible transformation of material size. To overcome the internal cohesive forces of materials, external forces must be applied. The required hammer hardness and toughness vary depending on material hardness and block size. For harder materials, the hammer should have higher hardness, while for larger material blocks, higher toughness is essential.
The Impact of Crusher Size on Hammer Selection
The size of the crusher also affects hammer selection:
Larger crushers require heavier hammers.
Bigger material blocks generate a greater impact load on the hammer.
Toughness should be prioritized first, followed by hardness improvement to enhance durability.
How to Use the Crusher Hammer Correctly
After selecting a suitable hammer head, proper usage is key to extending its service life. Here are some best practices:
Rotate the Hammer Surface – Timely replacement of the wear-resistant surface helps slow down wear.
Monitor Wear Levels – A set of hammers crushing 120,000–140,000 tons of limestone should be rotated, placing less-worn hammers from the center to the sides.
Adapt to Different Working Conditions – Adjust strategies based on varying operational factors to prolong hammer lifespan.
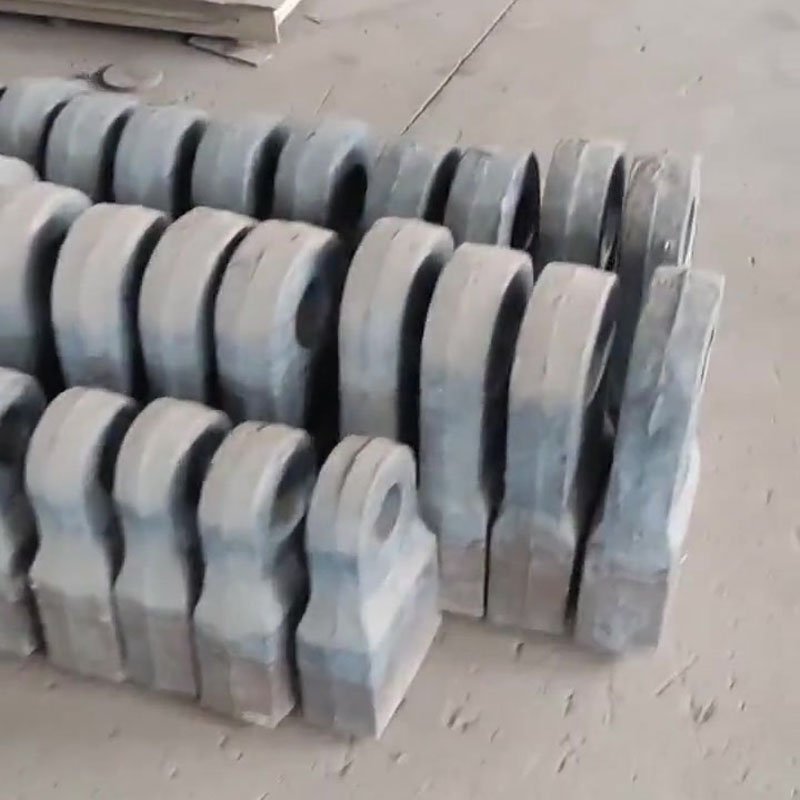
Final Recommendations
If possible, visit the crusher hammer manufacturer to inspect product quality before purchasing. Avoid making blind selections. Understanding the working conditions and wear mechanism will help in choosing the most suitable hammer material, ensuring optimal performance and longevity.